- Forum
- categories
- Sanitation systems
- Faecal sludge management (FSM)
- Faecal sludge transport (including emptying of pits and septic tanks, transfer stations)
- The excrevator (power auger) to empty pits (North Carolina State University, USA) - now field testing
The excrevator (power auger) to empty pits (North Carolina State University, USA) - now field testing
66.7k views
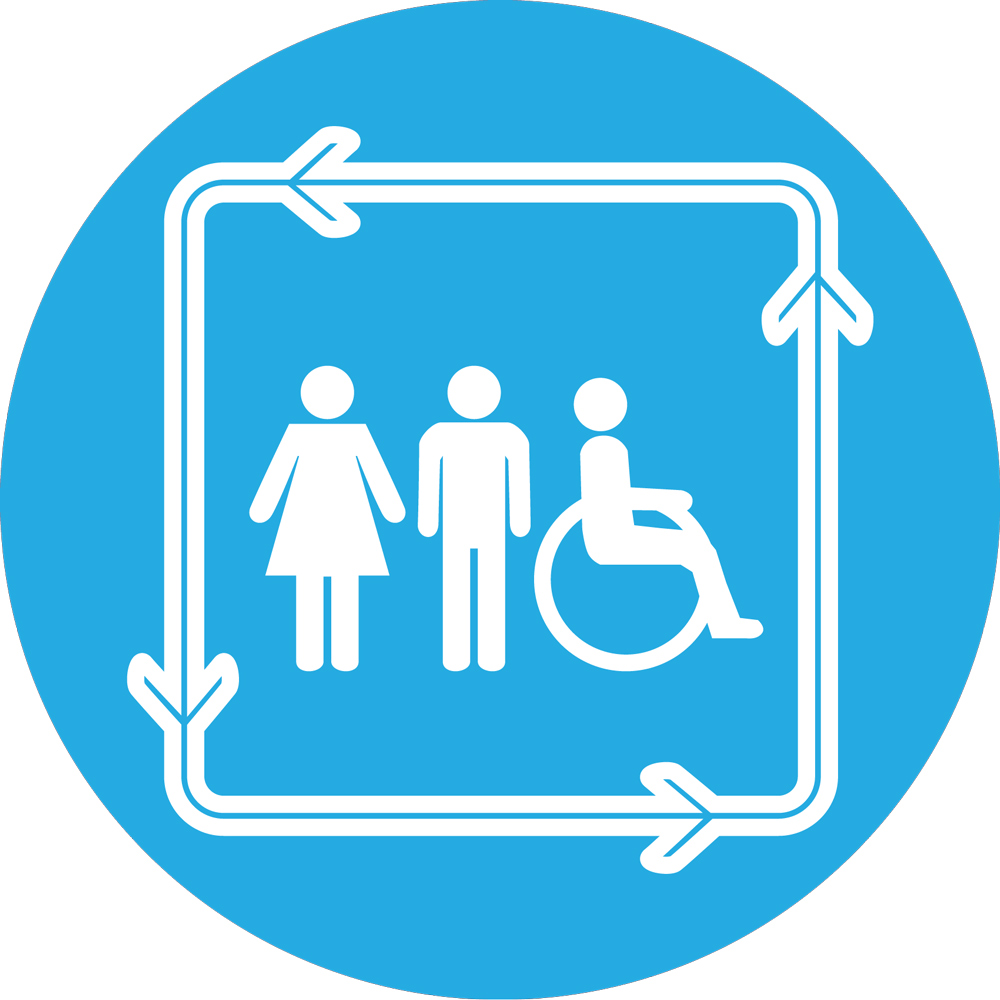
- jonpar
-
- As part of the Engineering team, my role at IMC is to lead on the delivery of projects requiring specific expertise on urban sanitation (including excreta/waste/wastewater/stormwater management) focusing on technical, institutional and financial aspects in project design and implementation.
Less- Posts: 223
- Karma: 24
- Likes received: 87
Re: Power auger modification to empty pits (North Carolina State University, USA and South Africa)
many thanks Frances, I am very interested in the developments that you report. We are on the verge of making formal announcement of the third Fecal Sludge Management International Conference to be held in Hanoi next year in January and I hope that you will come to present and we can discuss further. I do note that that on your website that the challenges that you face including emptying dry pits (non-flowing), and dealing with trash that is also found in the pits. This is the point that I was raising. But if this technology can shift concrete - see then I am sure it can deal with fecal sludge. But the limitation here will be putting the motor and drive directly on the end of the auger and maybe there is a need to design it so that the drive is on a cart. best regards, Jonathan
Dr. Jonathan Parkinson
Principal Consultant – Water and Sanitation
IMC Worldwide Ltd, Redhill, United Kingdom
Email: This email address is being protected from spambots. You need JavaScript enabled to view it.
Skype : jonathanparkinson1
Principal Consultant – Water and Sanitation
IMC Worldwide Ltd, Redhill, United Kingdom
Email: This email address is being protected from spambots. You need JavaScript enabled to view it.
Skype : jonathanparkinson1
The topic has been locked.
Re: Power auger modification to empty pits (North Carolina State University, USA and South Africa)
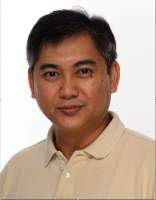
Oh, and we are now using a hydraulic motor powered by a 11 HP engine. That way, the motor head is lighter, and the engine can actually be 30 ft away (length of hydraulic hose). The other advantage of this is that we can reverse the rotation in case of jamming with big pieces of trash.
Francis de los Reyes III
Professor/TED Fellow
Professor/TED Fellow
The topic has been locked.
Re: Power auger modification to empty pits (North Carolina State University, USA and South Africa)
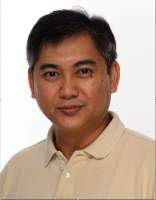
Jonathan,
Not sure which video you looked at, but there are several versions of the machine. Here's another video of the machine on dairy waste (no water added).
pitexcrevator.wordpress.ncsu.edu/the-excrevator/
Not sure which video you looked at, but there are several versions of the machine. Here's another video of the machine on dairy waste (no water added).
pitexcrevator.wordpress.ncsu.edu/the-excrevator/
Francis de los Reyes III
Professor/TED Fellow
Professor/TED Fellow
The topic has been locked.
Re: Power auger modification to empty pits (North Carolina State University, USA and South Africa)
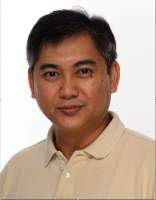
A brief update on our project:
Reliable and Hygienic Pit Emptying using Modified Screw Augers (The Excrevator)
We have received Phase II funding from the Bill and Melinda Gates Foundation to continue the work to improve the screw auger and test it in Malawi and South Africa. We have given it a name- 'The Pit Excrevator'
More information on the project is here: pitexcrevator.wordpress.ncsu.edu
Project Description:
Building on our Phase I results, we will continue to improve and develop a low-cost, portable auger-based technology that can reliably and hygienically empty a wide variety of pit latrines and septic tanks (pits) containing wastes with a range of moisture contents. Thus one machine can be used in watery, low solids pits (e.g, as occur in Malawi), and high solids and trash pits (e.g., as occur in eThekwini municipality in South Africa). We envision that a successful device will be used by local entrepreneurs or local governments in emptying pits, thus reducing the dangerous, and often unhygienic practice of manual pit emptying.
In Phase II, we will look at pit emptying approaches as a system so that a range of pit latrines with varying characteristics can be safely and effectively emptied. Using the power auger as the base, we will continue to improve and develop the technology and rethink current pit emptying strategies to improve performance in emptying pit contents from high water sludge to high solid waste material.
We will test the modified equipment prototypes in both Malawi and South Africa. The former will represent a location with more watery pits; the latter has VIPs that are both wet and dry, and often have high trash content. For our purposes, we define dry pits as having the moisture content of typical fresh fecal material or higher (>65% moisture; UKZN data). Both Malawi and SA are areas with a high demand for new pit emptying technologies. We will begin pushing the technology/operation packages to the field by consulting with private pit emptiers, and using their feedback to improve the screw auger design in an iterative process. We will leave the prototypes with entrepreneurs and our partners for long-term testing and collect feedback on long-term performance.
The objectives for Phase II are:
1. Develop the optimized extraction auger as a base technology for emptying pits with a wide range of contents.
2. Deploy and test the comprehensive pit emptying system in Malawi (University of Mzuzu, with Dr. Rochelle Holm) and South Africa (University of KwaZulu-Natal, with Prof. Chris Buckley)
So far, we are now in Prototype 3. The new Excrevator is now easier to move around and transport, with a built-in dolly, a new auger material, and new "controls" for variable speed and reverse rotation for unclogging jams. Below is a photo.
Here are the current stats:
Capital cost- $1,000 to $3,000 (the main cost is the power source, this can be bought locally)
Operating cost - main cost is petrol (1 L per pit) and maintenance; we estimate $5-20 per day
Life expectancy - 5 -10 years
Flow rates of 50 - 125 Liters per minute, depending on the material, so a 1 m3 pit can be emptied in 0.5 to 1.5 hours
One person can operate the machine, another person to handle waste collection
We've talked to private pit emptiers in SA, and the feedback is up to $2,000 to 3,000 dollars, if the machine will enable them to empty 1-2 more pits a day, they are interested in purchasing and using
We are currently testing in an experimental pit with various materials, including bentonite slurries with trash.
A paper in JWASH describing the initial prototype is also now in press. Please let me know if you have any questions.
Reliable and Hygienic Pit Emptying using Modified Screw Augers (The Excrevator)
We have received Phase II funding from the Bill and Melinda Gates Foundation to continue the work to improve the screw auger and test it in Malawi and South Africa. We have given it a name- 'The Pit Excrevator'

More information on the project is here: pitexcrevator.wordpress.ncsu.edu
Project Description:
Building on our Phase I results, we will continue to improve and develop a low-cost, portable auger-based technology that can reliably and hygienically empty a wide variety of pit latrines and septic tanks (pits) containing wastes with a range of moisture contents. Thus one machine can be used in watery, low solids pits (e.g, as occur in Malawi), and high solids and trash pits (e.g., as occur in eThekwini municipality in South Africa). We envision that a successful device will be used by local entrepreneurs or local governments in emptying pits, thus reducing the dangerous, and often unhygienic practice of manual pit emptying.
In Phase II, we will look at pit emptying approaches as a system so that a range of pit latrines with varying characteristics can be safely and effectively emptied. Using the power auger as the base, we will continue to improve and develop the technology and rethink current pit emptying strategies to improve performance in emptying pit contents from high water sludge to high solid waste material.
We will test the modified equipment prototypes in both Malawi and South Africa. The former will represent a location with more watery pits; the latter has VIPs that are both wet and dry, and often have high trash content. For our purposes, we define dry pits as having the moisture content of typical fresh fecal material or higher (>65% moisture; UKZN data). Both Malawi and SA are areas with a high demand for new pit emptying technologies. We will begin pushing the technology/operation packages to the field by consulting with private pit emptiers, and using their feedback to improve the screw auger design in an iterative process. We will leave the prototypes with entrepreneurs and our partners for long-term testing and collect feedback on long-term performance.
The objectives for Phase II are:
1. Develop the optimized extraction auger as a base technology for emptying pits with a wide range of contents.
2. Deploy and test the comprehensive pit emptying system in Malawi (University of Mzuzu, with Dr. Rochelle Holm) and South Africa (University of KwaZulu-Natal, with Prof. Chris Buckley)
So far, we are now in Prototype 3. The new Excrevator is now easier to move around and transport, with a built-in dolly, a new auger material, and new "controls" for variable speed and reverse rotation for unclogging jams. Below is a photo.
Here are the current stats:
Capital cost- $1,000 to $3,000 (the main cost is the power source, this can be bought locally)
Operating cost - main cost is petrol (1 L per pit) and maintenance; we estimate $5-20 per day
Life expectancy - 5 -10 years
Flow rates of 50 - 125 Liters per minute, depending on the material, so a 1 m3 pit can be emptied in 0.5 to 1.5 hours
One person can operate the machine, another person to handle waste collection
We've talked to private pit emptiers in SA, and the feedback is up to $2,000 to 3,000 dollars, if the machine will enable them to empty 1-2 more pits a day, they are interested in purchasing and using
We are currently testing in an experimental pit with various materials, including bentonite slurries with trash.
A paper in JWASH describing the initial prototype is also now in press. Please let me know if you have any questions.
Francis de los Reyes III
Professor/TED Fellow
Professor/TED Fellow
Attachments:
-
NewScrewer...olly.jpg (Filesize: 23KB)
The topic has been locked.
- jonpar
-
- As part of the Engineering team, my role at IMC is to lead on the delivery of projects requiring specific expertise on urban sanitation (including excreta/waste/wastewater/stormwater management) focusing on technical, institutional and financial aspects in project design and implementation.
Less- Posts: 223
- Karma: 24
- Likes received: 87
Re: Power auger modification to empty pits (North Carolina State University, USA and South Africa)
Dear Frances, I had a look at the video and I thought that you need a more powerful motor. I think the value of the auger is the fact that it has the capacity to remove consolidated/compacted sludge. The one you were testing didn't look like it had such a capacity and you were adding water to create a mixture which looked to me more suitable for pumping. I may be wrong but that was my observation. best regards, Jonathan
Dr. Jonathan Parkinson
Principal Consultant – Water and Sanitation
IMC Worldwide Ltd, Redhill, United Kingdom
Email: This email address is being protected from spambots. You need JavaScript enabled to view it.
Skype : jonathanparkinson1
Principal Consultant – Water and Sanitation
IMC Worldwide Ltd, Redhill, United Kingdom
Email: This email address is being protected from spambots. You need JavaScript enabled to view it.
Skype : jonathanparkinson1
The topic has been locked.
Re: Power auger modification to empty pits (North Carolina State University, USA and South Africa)
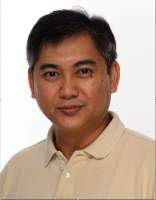
Hi Jonathan,
Thanks! We need to discuss and put our heads together - as you said, this is not an easy task!
I will put up an update in a separate post.
Regards,
Francis
Thanks! We need to discuss and put our heads together - as you said, this is not an easy task!
I will put up an update in a separate post.
Regards,
Francis
Francis de los Reyes III
Professor/TED Fellow
Professor/TED Fellow
The topic has been locked.
- jonpar
-
- As part of the Engineering team, my role at IMC is to lead on the delivery of projects requiring specific expertise on urban sanitation (including excreta/waste/wastewater/stormwater management) focusing on technical, institutional and financial aspects in project design and implementation.
Less- Posts: 223
- Karma: 24
- Likes received: 87
Re: Power auger modification to empty pits (North Carolina State University, USA and South Africa)
Dear Francis,
Very interested to receive an update on this as I have thought for quite a while that an system based on an auger (Archimedes screw) to desludge consolidated sludge sounds like a very promising approach due to the limitations of other mechanisms to extract sludge from pits.
Look forward to hearing from you.
Jonathan
Very interested to receive an update on this as I have thought for quite a while that an system based on an auger (Archimedes screw) to desludge consolidated sludge sounds like a very promising approach due to the limitations of other mechanisms to extract sludge from pits.
Look forward to hearing from you.
Jonathan
Dr. Jonathan Parkinson
Principal Consultant – Water and Sanitation
IMC Worldwide Ltd, Redhill, United Kingdom
Email: This email address is being protected from spambots. You need JavaScript enabled to view it.
Skype : jonathanparkinson1
Principal Consultant – Water and Sanitation
IMC Worldwide Ltd, Redhill, United Kingdom
Email: This email address is being protected from spambots. You need JavaScript enabled to view it.
Skype : jonathanparkinson1
The topic has been locked.
Re: Power auger modification to empty pits (North Carolina State University, USA and South Africa)
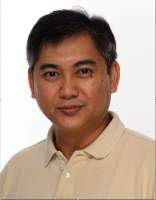
Hi Sudhir!
I hope everything is going well!
The recycle was really just so we can demonstrate the technology using one vessel- there's really no recycle in actual operation (pit contents go from the pit to the collection vessel).
Enjoy summer!
Regards,
Francis
I hope everything is going well!
The recycle was really just so we can demonstrate the technology using one vessel- there's really no recycle in actual operation (pit contents go from the pit to the collection vessel).
Enjoy summer!
Regards,
Francis
Francis de los Reyes III
Professor/TED Fellow
Professor/TED Fellow
The topic has been locked.
Re: Power auger modification to empty pits (North Carolina State University, USA and South Africa)
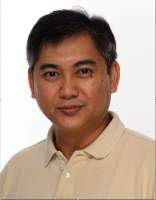
Hi Patricia,
Thanks for the questions! Below are my responses:
During the process of emptying, do you have any problems with odor? In case you have, do you have any methods to reduce the escape of bad odors?
The nice thing about the screw auger is that the pit contents travel through an enclosed tube to the collecting drum. So whatever odors are really from the pit and the vessels being filled. We recommend wearing at least dust masks as PPE when opening pits anyway, as a precaution against Ascaris eggs in the air. Respirators with with organic (charcoal) cartridges would mitigate odors.
• How many liters of fuel is consumed by the gasoline auger and the hydraulic motor for emptying a regular container in normal conditions? Do you think that the cost aim of 5 cents per user per day set by the Bill and Melinda Gates Foundation can be achieved?
If I had to guess, I would say that we used a liter of fuel per pit minimum.
The 5 cents per user per day doesn't really apply to pit emptying. Pit emptying rates vary depending on country (e.g., $160-180 in eThekwini municipality in S. Africa, lower in other countries with manual emptying of liquid waste). We can calculate for a pit serving say 8 people, and pit emptying is needed every 5 years, so it's $160/8 people/365 days/5 years so roughly 1 cent a day per person in eThekwini. This means that the rest of the toilet should only cost 4 cents per user per day if we want to keep total costs to 5 cents.
• You commented that the latrines present a wide range of variables, so different types of auger drills equipment are requested depending of the density and viscosity of the product. Do you think that it would be possible to design a model capable to face several kinds of densities in order to minimize costs? Could this be a real possibility?
This is our current directive. To end up with equipment that will handle a range of variables. I think we may end up with a two step process: a mixing operation to homogenize the contents followed by an emptying operation. We will be doing this research and development in Phase II.
• Besides, during the modifying and technological development phase, did you consider the possibility of using another kind of energy source to run the auger?
We used an electric motor in the lab and a direct drive gasoline engine. The current setup uses a gasoline engine driving a hydraulic pump. The pump drives a hydraulic motor mounted to the auger via hoses to reduce the weight of the hand-held auger. It would certainly be possible to drive the pump using a diesel or kerosene engine. We found that the auger must have a rotational speed of at least 350 rpm, which rules out any sort of hand crank.
A second design requirement was that the auger have a reverse gear to clear jams. Hydraulics were the easiest method of providing the required speed and reverse. We also fabricated a direct drive gasoline engine with reversing gearbox that we did not have time to test during phase I.
I hope this reply answers your questions! Please let me know if you need more info.
Thanks!
Francis
Thanks for the questions! Below are my responses:
During the process of emptying, do you have any problems with odor? In case you have, do you have any methods to reduce the escape of bad odors?
The nice thing about the screw auger is that the pit contents travel through an enclosed tube to the collecting drum. So whatever odors are really from the pit and the vessels being filled. We recommend wearing at least dust masks as PPE when opening pits anyway, as a precaution against Ascaris eggs in the air. Respirators with with organic (charcoal) cartridges would mitigate odors.
• How many liters of fuel is consumed by the gasoline auger and the hydraulic motor for emptying a regular container in normal conditions? Do you think that the cost aim of 5 cents per user per day set by the Bill and Melinda Gates Foundation can be achieved?
If I had to guess, I would say that we used a liter of fuel per pit minimum.
The 5 cents per user per day doesn't really apply to pit emptying. Pit emptying rates vary depending on country (e.g., $160-180 in eThekwini municipality in S. Africa, lower in other countries with manual emptying of liquid waste). We can calculate for a pit serving say 8 people, and pit emptying is needed every 5 years, so it's $160/8 people/365 days/5 years so roughly 1 cent a day per person in eThekwini. This means that the rest of the toilet should only cost 4 cents per user per day if we want to keep total costs to 5 cents.
• You commented that the latrines present a wide range of variables, so different types of auger drills equipment are requested depending of the density and viscosity of the product. Do you think that it would be possible to design a model capable to face several kinds of densities in order to minimize costs? Could this be a real possibility?
This is our current directive. To end up with equipment that will handle a range of variables. I think we may end up with a two step process: a mixing operation to homogenize the contents followed by an emptying operation. We will be doing this research and development in Phase II.
• Besides, during the modifying and technological development phase, did you consider the possibility of using another kind of energy source to run the auger?
We used an electric motor in the lab and a direct drive gasoline engine. The current setup uses a gasoline engine driving a hydraulic pump. The pump drives a hydraulic motor mounted to the auger via hoses to reduce the weight of the hand-held auger. It would certainly be possible to drive the pump using a diesel or kerosene engine. We found that the auger must have a rotational speed of at least 350 rpm, which rules out any sort of hand crank.
A second design requirement was that the auger have a reverse gear to clear jams. Hydraulics were the easiest method of providing the required speed and reverse. We also fabricated a direct drive gasoline engine with reversing gearbox that we did not have time to test during phase I.
I hope this reply answers your questions! Please let me know if you need more info.
Thanks!
Francis
Francis de los Reyes III
Professor/TED Fellow
Professor/TED Fellow
The following user(s) like this post: cecile
You need to login to reply
The topic has been locked.
Re: Power auger modification to empty pits (North Carolina State University, USA and South Africa)
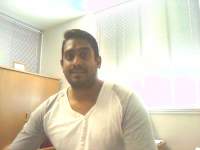
Dear Francis
Nice to see the video. Wanted to ask how long run the recycle and if you find any difference in emptying with & without recycle start-up.
My friends think I am it strange as I can eat and watch these type of videos for fun at the same time.
Nice to see the video. Wanted to ask how long run the recycle and if you find any difference in emptying with & without recycle start-up.
My friends think I am it strange as I can eat and watch these type of videos for fun at the same time.
Physical Address:
Water Research Commission, 4 Daventry Road, Lynnwood Bridge Office Park, Bloukrans Building, Pretoria.
Postal Address:
Private Bag X03
GEZINA, 0031, South Africa
email: This email address is being protected from spambots. You need JavaScript enabled to view it.
mobile: +27 (0)60 502 1841
Water Research Commission, 4 Daventry Road, Lynnwood Bridge Office Park, Bloukrans Building, Pretoria.
Postal Address:
Private Bag X03
GEZINA, 0031, South Africa
email: This email address is being protected from spambots. You need JavaScript enabled to view it.
mobile: +27 (0)60 502 1841
The topic has been locked.
- Patty
-
- Environmental Scientist and SEI intern in sanitation issues.
Less- Posts: 4
- Likes received: 0
Re: Power auger modification to empty pits (North Carolina State University, USA and South Africa)
Dear Francis,
Thank you very much for sharing your project and visual material with us. This is an interesting project since safe and hygienic pit emptying development is well needed.
During the reading some questions/ideas came to me:
• During the process of emptying, do you have any problems with odor? In case you have, do you have any methods to reduce the escape of bad odors?
• How many liters of fuel is consumed by the gasoline auger and the hydraulic motor for emptying a regular container in normal conditions? Do you think that the cost aim of 5 cents per user per day set by the Bill and Melinda Gates Foundation can be achieved?
• You commented that the latrines present a wide range of variables, so different types of auger drills equipment are requested depending of the density and viscosity of the product. Do you think that it would be possible to design a model capable to face several kinds of densities in order to minimize costs? Could this be a real possibility?
• Besides, during the modifying and technological development phase, did you consider the possibility of using another kind of energy source to run the auger?
Looking forward to hear from you!
Best Regards,
Patricia
Thank you very much for sharing your project and visual material with us. This is an interesting project since safe and hygienic pit emptying development is well needed.
During the reading some questions/ideas came to me:
• During the process of emptying, do you have any problems with odor? In case you have, do you have any methods to reduce the escape of bad odors?
• How many liters of fuel is consumed by the gasoline auger and the hydraulic motor for emptying a regular container in normal conditions? Do you think that the cost aim of 5 cents per user per day set by the Bill and Melinda Gates Foundation can be achieved?
• You commented that the latrines present a wide range of variables, so different types of auger drills equipment are requested depending of the density and viscosity of the product. Do you think that it would be possible to design a model capable to face several kinds of densities in order to minimize costs? Could this be a real possibility?
• Besides, during the modifying and technological development phase, did you consider the possibility of using another kind of energy source to run the auger?
Looking forward to hear from you!
Best Regards,
Patricia
Patricia Villarrubia Gomez
Intern
Stockholm Environment Institute
www.sei-international.org
Kräftriket 2B
10 691 Srockholm, Sweden
Skype: patty_villarrubia
Intern
Stockholm Environment Institute
www.sei-international.org
Kräftriket 2B
10 691 Srockholm, Sweden
Skype: patty_villarrubia
The topic has been locked.
Field Testing in South Africa
In March 2013, our modified design was tested on a range of wet and dry pits in Pietermaritzburg, South Africa, with the help of Partners in Development. Field testing of the extraction auger generated the following conclusions.
1. The hydraulic powered extraction auger was easily carried to all of the pits investigated. While it was not possible to drive a vehicle close to many latrines, access with the equipment was not a problem. Fig 3 shows use of the extraction auger down a narrow alley.
2. Clogging with trash and other debris was not a problem. Reversing the auger ejected most debris. While elastic bands (presumably from disposable diapers) did occasionally get wrapped around the auger, they did not result in jamming of the equipment. When trash was caught in the auger, the machine could be easily reversed, ejecting most of the trash and other debris.
3. The machine was very effective at pumping medium viscosity wastes containing a mixture of liquid and solid material. Fig 4 shows five containers pumped out of a pit in Durban, SA after about 20 minutes operation.
4. The equipment was not very effective in removing watery, low viscosity waste. This characteristic was identified early in the laboratory testing. However in this field, it is not a significant drawback since other available technologies (Gulper, Vacutug or a simple trash pump) are effective in removing this type of waste.
5. The equipment was not effective in removing solid waste in dry pits without some liquid material. The auger was able to drill into the solid waste. However, this just formed a ‘posthole’ in the non-flowing solid waste. Additional work is needed to develop an effective method to empty ‘dry’ pits. This could include mixing the solid waste with liquid, followed by augering or use of other equipment.
6. There is an incredible variation in the composition of waste in these pits. One pit may contain semi-solid material that is easily removed with the extraction auger, while another pit 30 m away contains very hard, floating material that is difficult to penetrate. No single technology will be appropriate for this wide range of conditions. To be effective, operators need a range of tools to manage the broad range of conditions encountered.
7. It is difficult to determine the amount and character of waste through the toilet, prior to breaking the pit seal. Assessment methods are needed to determine when pits need to be emptied and to identify the best approach for removing the waste. This evaluation needs to be performed through the toilet, without excavating the actual pit and breaking the seal.
The design developed in Phase I of this project was effective in emptying semi-solid waste from difficult to access pits, even when the pits contained trash and other debris. The extraction auger system has met all listed criteria for Technology Readiness Level ITRL) of 7. We have demonstrated the use of a fully functional prototype assembled from commercially available components in an operational environment (wet and dry pits in South Africa).
While the extraction auger was effective in emptying wet pits containing semi-solid sludge, additional work is needed to develop tools and procedures to safely and effectively empty the broad range of pits present in many areas. Needs identified in this project include:
• Modify our current design to improve the performance, durability and sanitary use of this equipment for pits containing semi-solid waste.
• Develop equipment to efficiently mix dense solid waste with liquid to form a semi-solid material that can be more easily extracted.
• Modify the existing auger design to facilitate its use with currently available vacuum technologies to remove both the dense material and free liquid from the pit.
• Develop methods to assess the amount of waste in a pit and its general composition without significant excavation or breaking the seal on the pit.
Great challenges remain in safely and effectively removing wastes from pits. A variety of different tools are needed to safely and effectively empty pits. Currently available vacuum technologies and the extraction auger developed in this project can help. However, additional tools and equipment are needed to expand the range of pits that can be emptied.
Waste extracted from pit in Durban, SA:
In March 2013, our modified design was tested on a range of wet and dry pits in Pietermaritzburg, South Africa, with the help of Partners in Development. Field testing of the extraction auger generated the following conclusions.
1. The hydraulic powered extraction auger was easily carried to all of the pits investigated. While it was not possible to drive a vehicle close to many latrines, access with the equipment was not a problem. Fig 3 shows use of the extraction auger down a narrow alley.
2. Clogging with trash and other debris was not a problem. Reversing the auger ejected most debris. While elastic bands (presumably from disposable diapers) did occasionally get wrapped around the auger, they did not result in jamming of the equipment. When trash was caught in the auger, the machine could be easily reversed, ejecting most of the trash and other debris.
3. The machine was very effective at pumping medium viscosity wastes containing a mixture of liquid and solid material. Fig 4 shows five containers pumped out of a pit in Durban, SA after about 20 minutes operation.
4. The equipment was not very effective in removing watery, low viscosity waste. This characteristic was identified early in the laboratory testing. However in this field, it is not a significant drawback since other available technologies (Gulper, Vacutug or a simple trash pump) are effective in removing this type of waste.
5. The equipment was not effective in removing solid waste in dry pits without some liquid material. The auger was able to drill into the solid waste. However, this just formed a ‘posthole’ in the non-flowing solid waste. Additional work is needed to develop an effective method to empty ‘dry’ pits. This could include mixing the solid waste with liquid, followed by augering or use of other equipment.
6. There is an incredible variation in the composition of waste in these pits. One pit may contain semi-solid material that is easily removed with the extraction auger, while another pit 30 m away contains very hard, floating material that is difficult to penetrate. No single technology will be appropriate for this wide range of conditions. To be effective, operators need a range of tools to manage the broad range of conditions encountered.
7. It is difficult to determine the amount and character of waste through the toilet, prior to breaking the pit seal. Assessment methods are needed to determine when pits need to be emptied and to identify the best approach for removing the waste. This evaluation needs to be performed through the toilet, without excavating the actual pit and breaking the seal.
The design developed in Phase I of this project was effective in emptying semi-solid waste from difficult to access pits, even when the pits contained trash and other debris. The extraction auger system has met all listed criteria for Technology Readiness Level ITRL) of 7. We have demonstrated the use of a fully functional prototype assembled from commercially available components in an operational environment (wet and dry pits in South Africa).
While the extraction auger was effective in emptying wet pits containing semi-solid sludge, additional work is needed to develop tools and procedures to safely and effectively empty the broad range of pits present in many areas. Needs identified in this project include:
• Modify our current design to improve the performance, durability and sanitary use of this equipment for pits containing semi-solid waste.
• Develop equipment to efficiently mix dense solid waste with liquid to form a semi-solid material that can be more easily extracted.
• Modify the existing auger design to facilitate its use with currently available vacuum technologies to remove both the dense material and free liquid from the pit.
• Develop methods to assess the amount of waste in a pit and its general composition without significant excavation or breaking the seal on the pit.
Great challenges remain in safely and effectively removing wastes from pits. A variety of different tools are needed to safely and effectively empty pits. Currently available vacuum technologies and the extraction auger developed in this project can help. However, additional tools and equipment are needed to expand the range of pits that can be emptied.
Waste extracted from pit in Durban, SA:
Francis de los Reyes III
Professor/TED Fellow
Professor/TED Fellow
Attachments:
-
picture.jpg (Filesize: 45KB)
The topic has been locked.
Share this thread:
- Forum
- categories
- Sanitation systems
- Faecal sludge management (FSM)
- Faecal sludge transport (including emptying of pits and septic tanks, transfer stations)
- The excrevator (power auger) to empty pits (North Carolina State University, USA) - now field testing
Recently active users. Who else has been active?
Time to create page: 0.077 seconds